Lean, mean machine
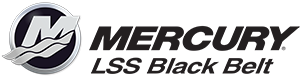
The managerial concept of Lean Six Sigma was instituted by Toyota to eliminate different types of waste, then was fine-tuned by major corporations such as Motorola and GE to focus on customer satisfaction, and shortly after was adopted by Mercury Marine with the goal of eliminating waste and maintaining critical quality.
Mercury’s Lean Six Sigma training provides opportunities to engage the minds of employees who can become project leaders by learning additional skills and earning “belts” with experience, much like in Judo.
Mercury Marine is one of only a few companies to produce black belt employees not just from manager positions, but also from its production workforce. Those who earn “black belt” status have become proven “masters” of the Lean Six Sigma methodology and lead projects, using what they learned daily and mentoring other workers with “green belt” status.
Applied to product design, manufacturing, planning, sales, distribution, and service, the benefits of Lean Six Sigma became evident over the years through improved product quality, better customer service, and lower costs. In 2006, with more than 700 Mercury employees trained, and by its 1,000th project, a savings of more than $74 million had been achieved.
Today, Lean Six Sigma project masters work in teams to assist departments in other efficiency programs, such as the “5S+1 for Safety” and a “Flow Analysis” program that traces the process of a component through all stages of its production, from die cast to machining to suppliers and the assembly line, where it becomes an integral piece of an engine.
Involving a wide range of people in the process helps diversify the input, and the results. “Those on the line for two or 20 years all have good ideas,” said one master. “Each participant sees the value stream — the whole chain of events before the product goes out the door to the customer.”
As the program has grown, cost savings were viewed as only one goal; the cultural transformation of the business was also significant — providing employees an opportunity to contribute to corporate philosophy as well as the bottom line.
5S+1 = Safety

One example of a Lean Six Sigma quality and efficiency management project at Mercury Marine is the recently implemented 5S+1 program. A team of eight trained productivity specialists led a team of supervisors and production personnel helping workers learn to analyze and suggest improvements for a better workplace.
- 5S+1 — provide an evaluation starting point.
- Sort — see what you need and don’t need.
- Shine — deep clean, remove clutter.
- Set in order — put back what is needed.
- Standardize — prioritize.
- Sustain — how do we maintain the system?
- +1 S for Safety
The overall goal is to create an environment that allows working more safely, more efficiently and more ergonomically.