Safety first
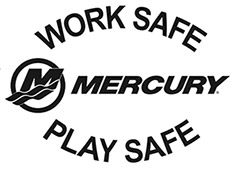
Making the most impressive marine performance products in the world isn’t enough. Mercury Marine also constantly strives to improve its performance in every facet of its business, and has earned a reputation as one of Wisconsin’s safest manufacturers.
One semi-recent example of the company’s workplace-safety records: Mercury Racing won the 2012 Wisconsin Manufacturers & Commerce Association’s annual safety award. The honor came on the heels of the racing division logging more than 1.6 million hours without a lost-time injury in 2012, earning the group the Brunswick Chairman’s Safety award for the third consecutive year.
That same year, Mercury’s steel investment-casting business compiled more than 4.5 years without a lost-time injury, earning another Brunswick Chairman’s Safety Award. Meanwhile, Mercury’s steel machining operation surpassed four years (1.63 million hours) and distribution operations accumulated more than 2 million hours without lost time due to injury.
These milestones were the products of initiatives implemented in 2000 with employee input on ways to improve on-the-job safety. In 2005, Mercury introduced its Health, Safety and Management Council to define safety processes and empower employees to work more safely. Soon after, the Safety Management System was formed to reinforce the council’s focus.
Today, operations staff meetings begin with a safety roundtable, where leaders share information about successful efforts to influence safety. Employees routinely conduct safety observations and are encouraged to identify areas for improvement. Mercury hosts an annual Health, Safety and Environmental Summit to develop safety leadership, share best practices and conduct annual planning sessions to improve safety.
Advancements in employee safety this decade started with investing more than $1 million to update and enhance Mercury’s emergency warning system, installation of 10 two-axis die sprayers to eliminate hand spraying to clean and lubricate tools, and the addition of extraction robots to 11 die-casting cells in the past three years. Numerous lift assists were added to engine assembly, and assembly carriers are designed to ergonomically adjust to each individual employee. Perhaps most importantly, employees were involved in the design and refinement of the systems, resulting in fewer manufacturing disruptions.
Race-proven low-emissions technology
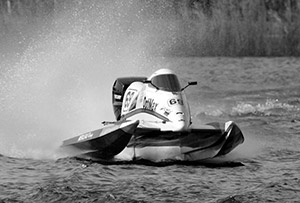
Proving new engine technology right on the racecourse is something Mercury Marine has accomplished throughout its 75 years of providing reliable marine propulsion.
At the grueling 24 Hours of Rouen endurance race in France in 1997, two new 200hp low- emissions, direct-fuel-injection, two-stroke outboards made history by finishing fourth and fifth overall and ahead of every boat powered by a competing engine company.
The new Mercury DFIs also burned half as much fuel as the Mercury S3000 outboards that claimed the top three positions in the race.
In 1999, the new OptiMax 200XS race engine finished third overall, ahead of all comparable-horsepower race outboards. In 2000, an OptiMax-powered two-boat team took the top two positions, beating higher horsepower engines, in part, by making fewer pit stops for fuel.
Mercury also set five bass boat, low-emissions speed records with OptiMax; first in 1996 to establish the low-emissions records, then again in 2002 to break those records with the latest OptiMax technology.