Corrosion Protection
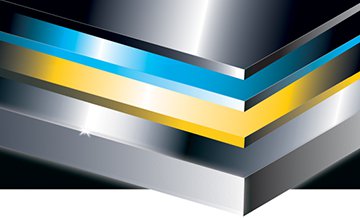
Key components receive an electro-chemical treatment called “hardcoat anodizing.” This coating increases corrosion resistance, resists wear, and provides better adhesion for paint.
- Protection starts with Mercury’s exclusive low-copper aluminum alloys.
- Iridite sealing provides a corrosion-resistant barrier before paint is applied.
- Electro Deposition Paint primer creates uniform coverage that seals out the environment.
- The powder paint top coat is harder, thicker and tougher than conventional paint.
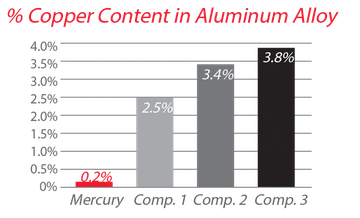
Most competitors use alloys with 2% to 4% copper content which will corrode faster than our Mercalloy®, XK360 or A356 alloys.
Alloys are a combination of aluminum, copper, silicon, and other elements. When immersed in water, electrons begin to flow within the material. Aluminum is corroded by the presence of copper. Low copper content reduces the opportunity for that interaction resulting in better strength and corrosion resistance.

Yellow indicates passageways treated with Mercury® Salt Shield coating.
- Provides industry-leading corrosion resistance in water-cooling passages.
- Flushed into the powerhead and water passages to protect the engine from the inside out.

Amount of stainless steel on a four-cylinder Verado® vs. competitive 150hp four-strokes.
Mercury outboards contain at least twice the amount of stainless steel as the competition. Hardened steel is friction welded to corrosion-fighting stainless steel, producing strong and reliable shafts. This ensures saltwater only comes in contact with stainless steel.