Lost Foam Casting: The technology behind the technology
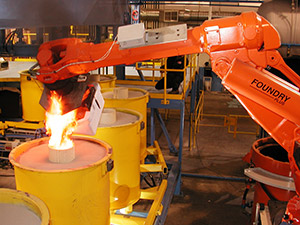
Using “lost-foam casting” to produce intricate, single-piece engine parts isn’t new, but Mercury Marine — as it has throughout its eight-decade history — put a new spin on improving the manufacturing technology to optimize its outboard technology and quality.
Mercury engineers found a way to create a vacuum path between the metal used to create a given part and the foam mold. The molten metal melts the foam and assumes its shape. The vacuum created by that process draws the liquid aluminum or steel through the form. The process creates an advantage over simply pouring the molten metal, which can cause the metal to settle unevenly in the mold.
By using a vacuum to draw the metal into the cavity-filled foam replica of the eventual part, Mercury improved the quality of the casting. Mercury Marine was awarded a United States patent for the process when it was proved reliable. Officially called the Vacuum Lift Foam Filled Casting Process, it has since become Mercury’s most economical way to produce premium quality castings.
The vacuum lift process creates a cost savings for Mercury because it allows casting to be accomplished with smaller amounts of steel, aluminum or other materials, resulting in reduced waste.
The process allowed Mercury Marine to change the way it does business with large steel mills. It allows small “heats” of “bearing quality” steel to be cast directly into crankshafts, connecting rods and other parts instead of being machined from forgings that come from large 100-ton heats of steel. Because Mercury can produce parts in smaller batches using The Vacuum Lift Foam Filled Casting Process, the company can switch over part production more frequently and easily to maintain pace with customer demand and maintain quality control.
With its heritage of improving on the best technology — in process and product — it’s no wonder Mercury Marine made lost-foam casting even more effective and efficient.
Boat brakes broke boats
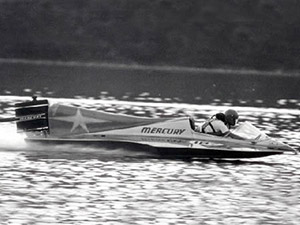
A commonly heard safety adage is “boats don’t have brakes,” but for a brief period in the mid-1970s, they did.
The key to winning tunnel boat races is how fast a driver can turn the boat, a technique akin to a “controlled spinout.” Using throttle and trim, a driver slows to the fastest safe speed to turn without barrel rolling the boat.
Mercury Racing developed a system that dropped a small metal plate from under each sponson “and almost threw you through the front of the boat,” said Reggie Fountain, a member of the Mercury factory team that eliminated two of the fastest Outboard Marine Corporation boats at the first race.
“I hit the brakes and damn near stopped,” Fountain said. “They ran into the back of my boat and just disintegrated.”
After only a few races, protests from competitors led to a ban on boat brakes. But that didn’t slow Team Mercury’s charge to victory one bit.